Hollow bars are fully threaded, “disposable” drill rods capable of drilling holes utilizing sacrificial bits that will advance the drill string to the required depth and then allow them to be grouted in place. This process creates the steel reinforcing portion of an anchor or pile. Hollow bar products are a valuable and multi-functional addition to the geotechnical contractor’s toolbox. They can be used as tie back or tie down anchors, rock anchors, soil nails and micropiles in a large array of challenging applications.
There are three basic types of drill bits for use with hollow bars. Versatile cross cut bits in carbide or hardened steel, button bits for intact rock in carbide or hardened steel and steel stepped clay bits for cohesive soils. The selection of the drill bit type and size is based on the material that is being drilled through and the desired borehole diameter. A larger borehole diameter provides greater load carrying capacity and greater grout cover. Grout cover protects the anchor rod from corroding. Depending on the actual soil type, a 2.5 inch diameter bit can produce a 6 to 8 inch diameter grout column.
Production rates are increased through the use of hollow bar systems, as compared to traditional solid bar anchors. This is especially true when drilling through “difficult conditions”. In sites with low headroom, large scale drilling rigs and hole casing systems can be avoided. With drill rigs where “through the head grouting” is not available, grout swivels can be used to retrofit standard rotary percussion drills.
Hollow Bar Corrosion Protection
The level of corrosion protection is dependent on the anticipated service life of the anchor, installation methods, and the corrosion potential (aggressiveness) of the environment. The FHWA has studied the effects of installation on both galvanized and epoxy coated bars as reported in FHWA CFL/TD10-002. This study revealed epoxy coatings were both partially and completely removed at the leading edge of the screw profile and around the couplings.
The installations were constructed using hollow bars as both the drill rod and reinforcement. The effects of the removal reduced the service life of the bar substantially by creating concentrated locations for potential corrosion. As such, the designer should evaluate all possibilities when determining the level of corrosion protection required.
Hot Dipped Galvanizing
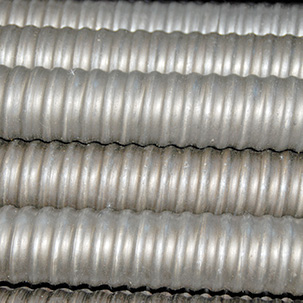
Hot dipped galvanizing is a form of galvanization and is the process of coating a base metal such as steel with molten zinc. The zinc acts as a sacrificial material to the steel. The galvanized coating is manufactured in accordance with ASTM A 53 standards and is more resistant to handling than epoxy coatings.
Sacrificial Steel
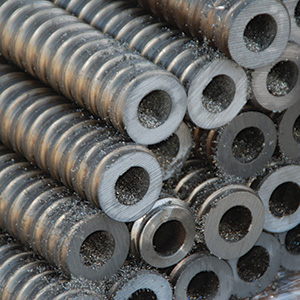
Using sacrificial steel as a form of corrosion protection requires a geotechnical evaluation of the corrosivity of the soils. The estimated loss of steel thickness is calculated and then the hollow bar is designed with the additional increase in thickness.
Download datasheet